Cirql
This is the moment the footwear industry has been waiting for: the arrival of less impactful materials that deliver on performance and are ready to scale globally. Focused on two ends of life – recyclable and compostable/biodegradable formulations, the trust, market-leading innovators at Cirql have brought us to this critical point in time.
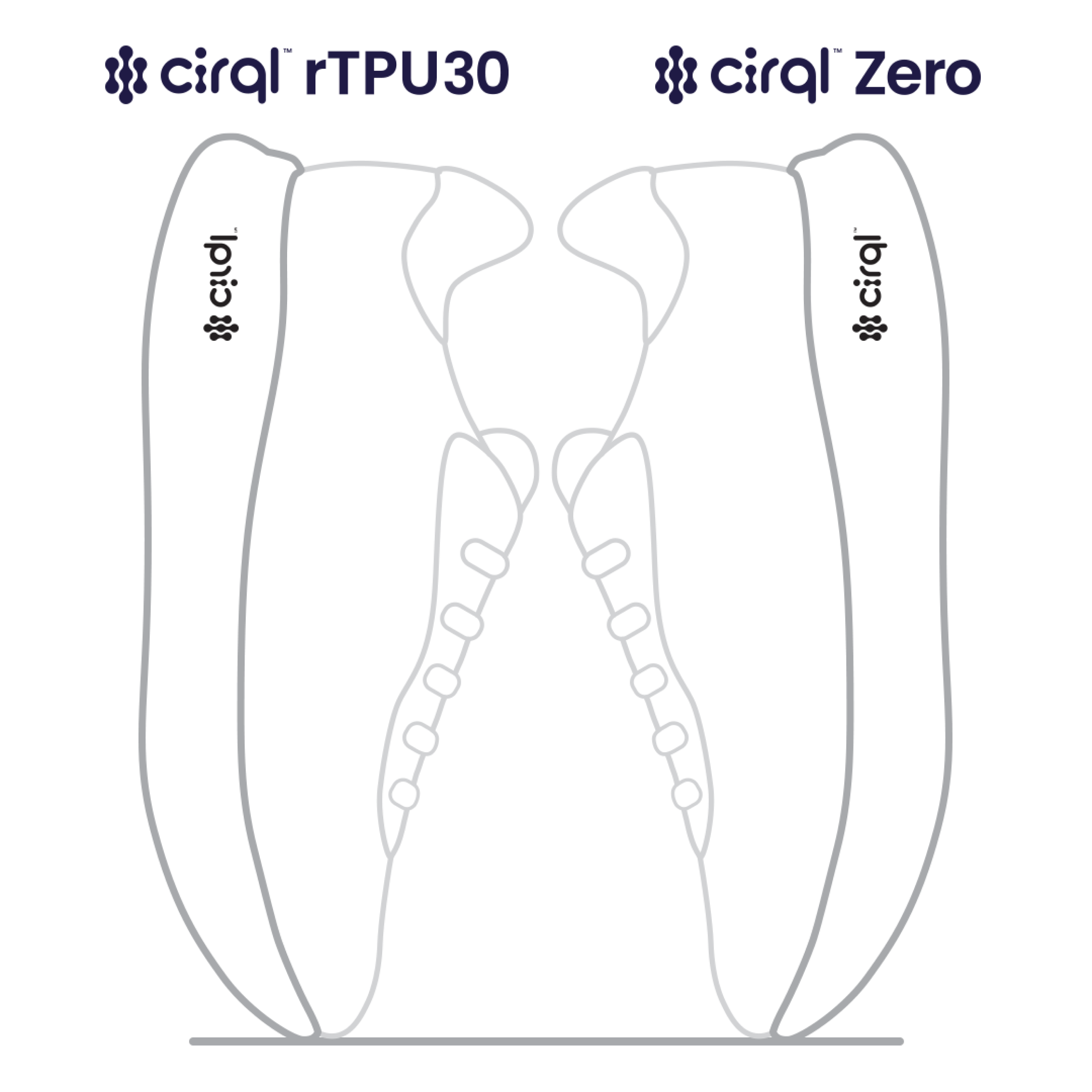
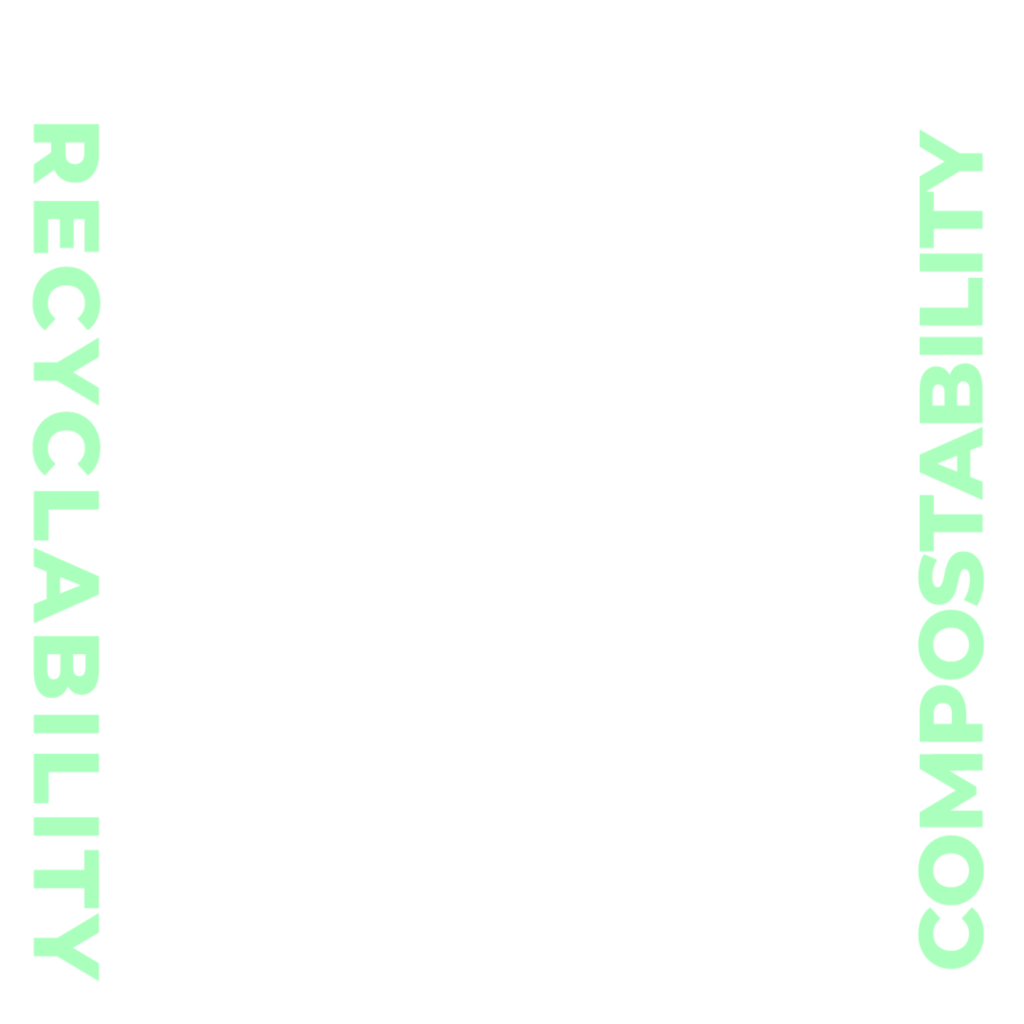
Make Your Mark By Not Leaving One
Made with our patented supercritical foaming process that uses Nitrogen gas and no added chemical foaming agents in production, both Cirql Zero and Cirql rTPU30 are globally scalable and ready to help brands reach their climate goals and lighten their impact.

- 30% Post-Consumer Recycled TPU
- 70% Virgin TPU
- 100% Recyclable at End of Life
- GRS Certified

- Low Density
- High Rebound
- Medium/Soft Cushioning
- Made from certified industrial compostable materials
OUR INDUSTRY HAS A
GROWING WASTE PROBLEM
We believe in challenging ourselves and the footwear industry to think differently—to create sustainable solutions that will lead us into true circularity.
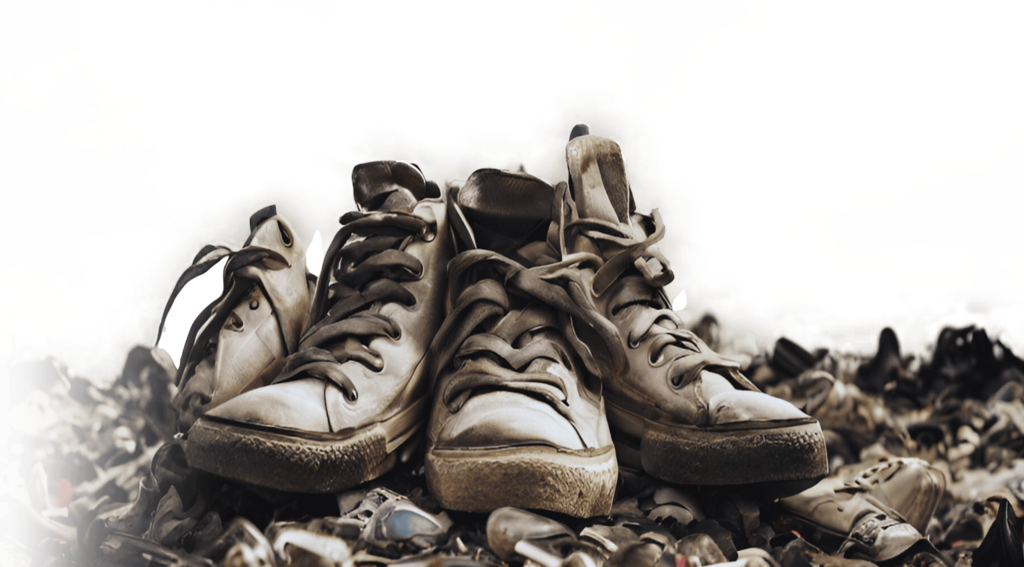
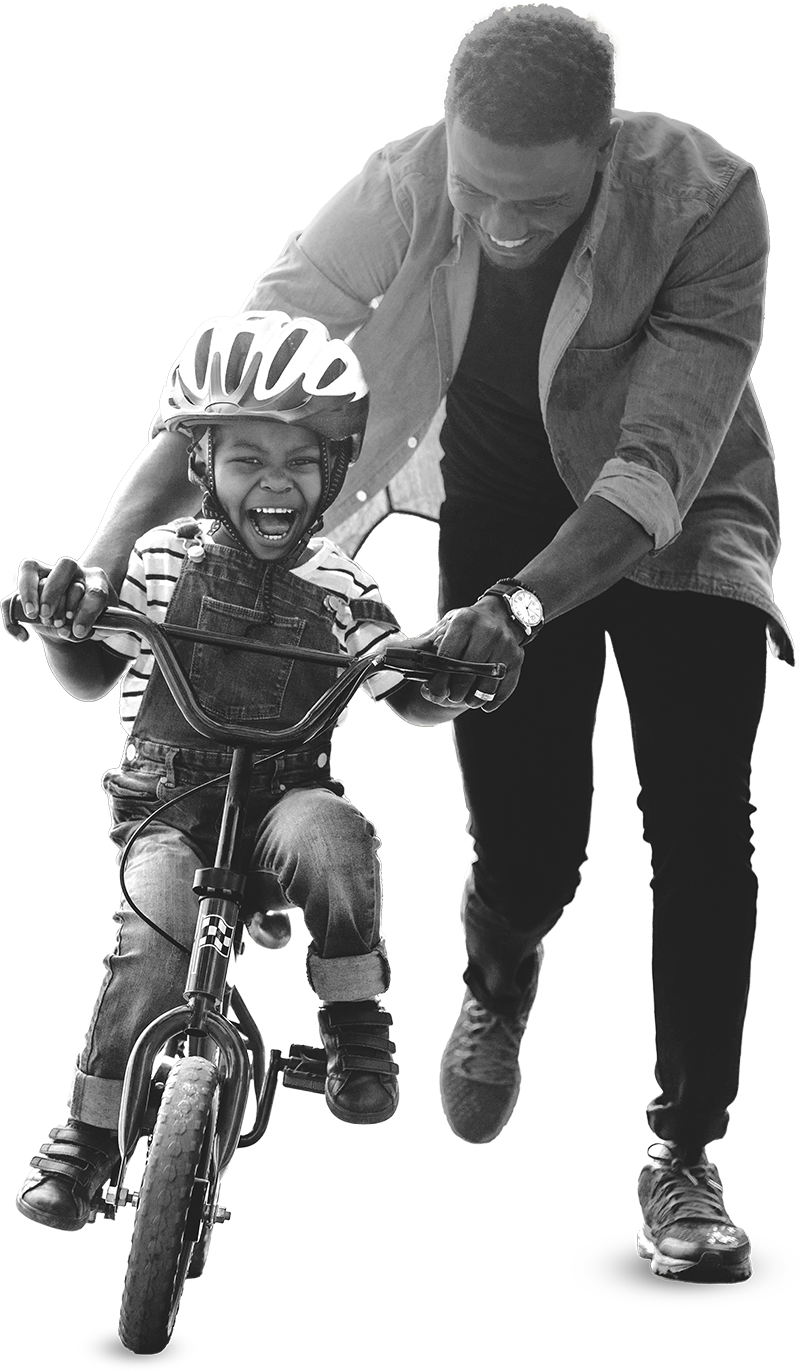
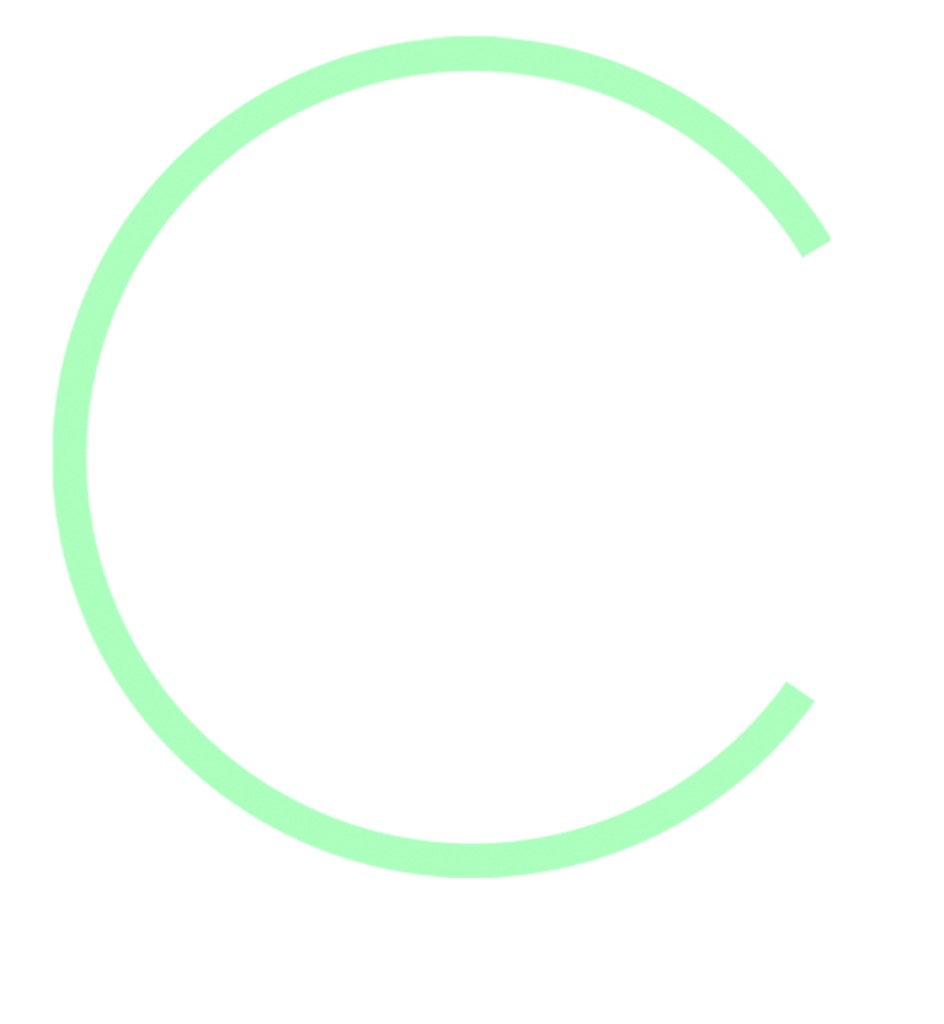
OUR VISION: LIGHTER
IMPACT WITH EVERY STEP
Cirql exists to help lead the footwear industry toward circularity and a more sustainable future while also helping to eliminate the use of toxic chemicals traditionally used in the footwear manufacturing process. Along with the introduction of our two flagship formulations representing two ends of life, we’re committed to create a suite of sustainable innovation solutions for the footwear industry. Our goal: to keep shoes out of landfills.
THE CIRQL STARTS AND
ENDS WITH YOU
We have arrived at a critical moment in circularity for the footwear industry. But the loop is not yet closed. We are now calling on footwear brands, retailers, and consumers to complete the Cirql for a brighter future.
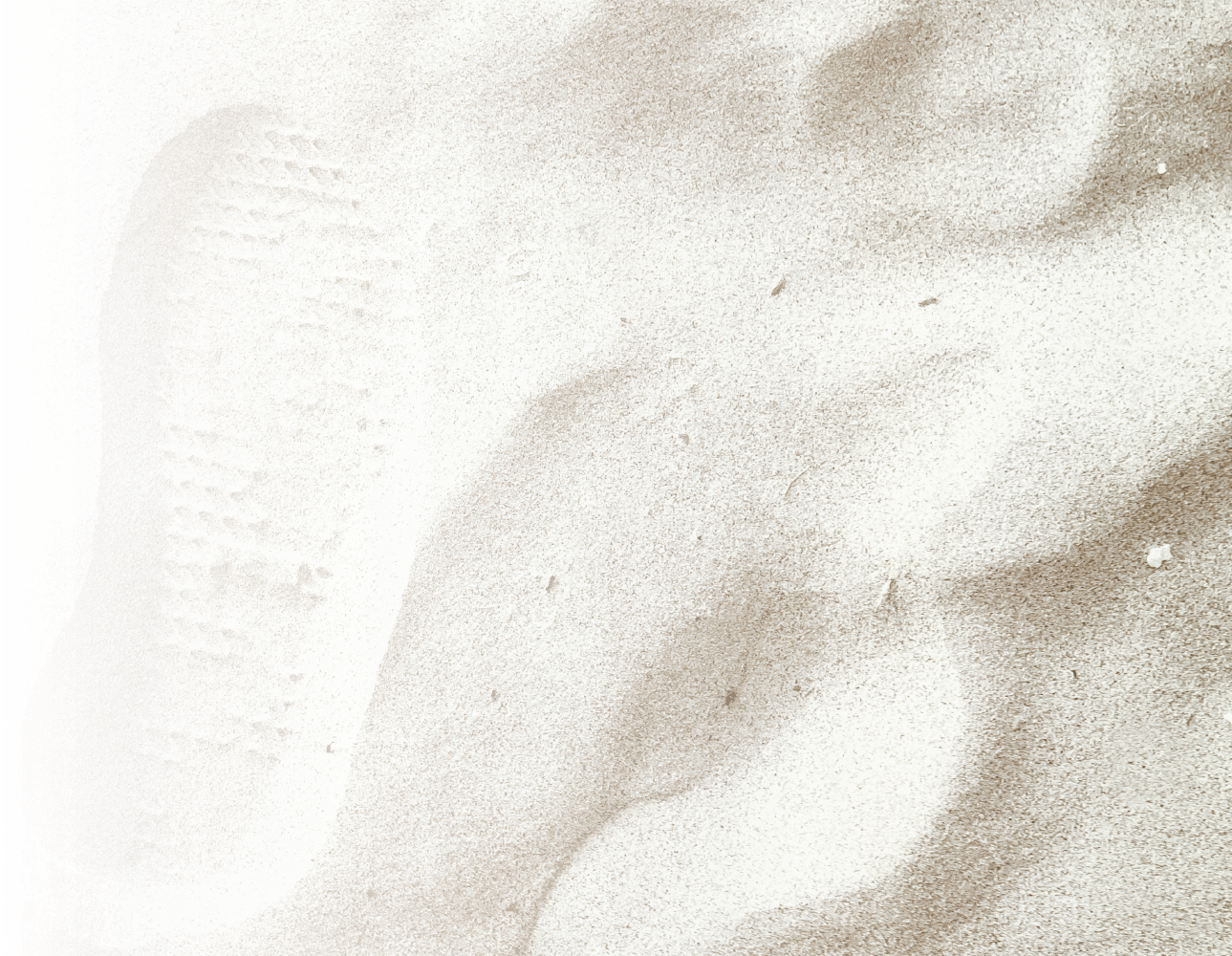
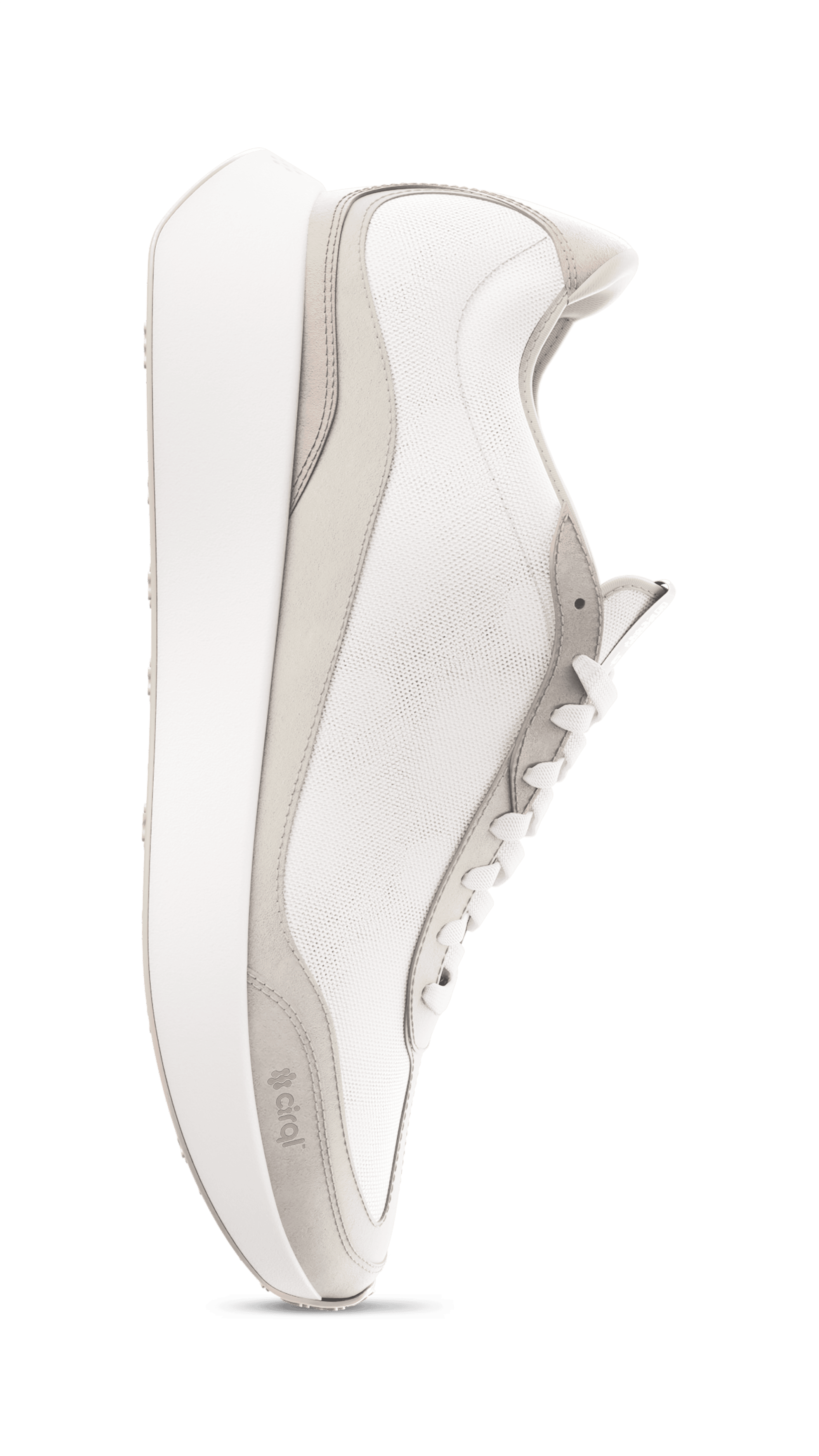
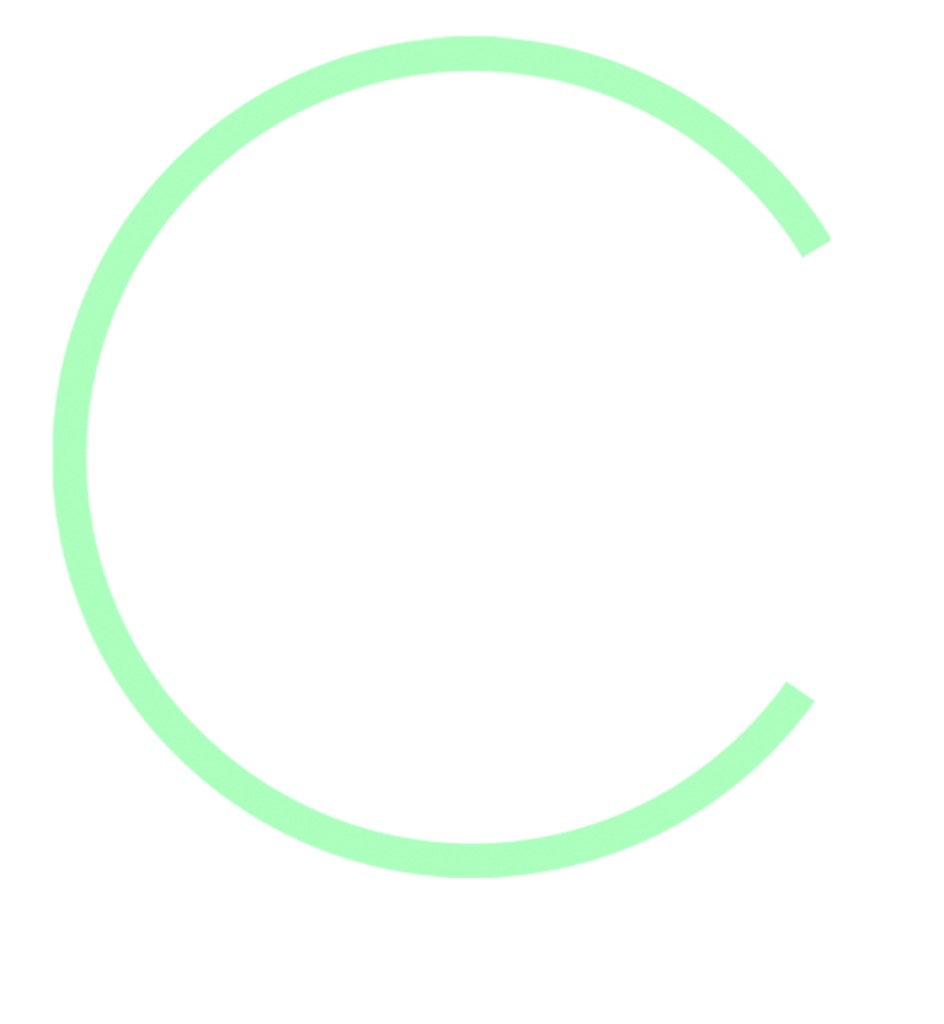